
Process
Agrifood:
- Dry ingredient handling, loading/unloading, crusher, grinder, sifting, dust collection, stockage (silos), mixing, separation, decantation, fermentation, pasteurization, brewing, maceration, distillation, evaporation, filtration, centrifugation, extrusion, drying, formulation, cooking, concentration, liquification, emulsification, clean-in-place, sterilization, food-grade clean steam, refrigeration, freezer, deep freezing
Pharmaceutical:
- Liquid, ointment and cream formulation, solid processing, aseptic processing, cytotoxic handling, lyophilisation, fermentation, cell culture, inactivation, chromatography, tangential filtration, centrifugation, microfiltration, clean-in-place and sterilization
Bioindustrial:
- Process scale-up, media preparation and sterilization, sterile and non-sterile fermentation, solid and liquid fermentation, batch, fed-batch and continuous fermentation, clean-in-place, centrifugation, decanter centrifuge, membrane technologies, filtration, homogenization, cell disruption, concentration, crystallisation, drying

Automation
- Control system architecture design
- Vision systems design and integration
- Robotic systems design and integration
- VFD design, configuration, integration
- PLC programming, integration, and migration (Allen-Bradley, Siemens, Schneider Electric)
- HMI programming, integration, and migration (Allen-Bradley, Siemens, Schneider Electric)
- SCADA programming and integration (Wonderware, FactoryTalk, iFix, Ignition)
- Clean room environmental monitoring system (EMS) design, programming, integration
- Alarm management, optimization, distribution (email, SMS, external systems)
- Plantwide cabling and installation design, including pharmaceutical clean rooms and food and beverage washdown areas
- Automation equipment/systems audit, risk-assessment, opportunity-assessment
- Hazardous area installations (flammable liquids and combustible dusts)
- Control panel, MCC, network, and power distribution panel design
- Equipment and control system design, specification, testing (FAT/SAT), integration, troubleshooting
- Thin client design, configuration, integration
- Data historian programming, integration, migration (Allen-Bradley, OSISoft Pi, Wonderware, Ignition)
- Virtualized deployment of automaton and enterprise application servers
- Instrumentation
- Design for remote access of automation equipment
- Design in compliance with UL 508A, NFPA70/NEC, 21 CFR Part 11
For integrated turnkey solutions : Laporte Integration
Industrial Technologies & Networking (IT/OT)
- Server room design
- Cabling, installation design
- Network audit, risk-assessment
- Virtualized infrastructure
- Redundant infrastructure
- Dashboards and KPI screens
- Firewalls and cyber security
- Databases and historians
- Integration between automation and business systems
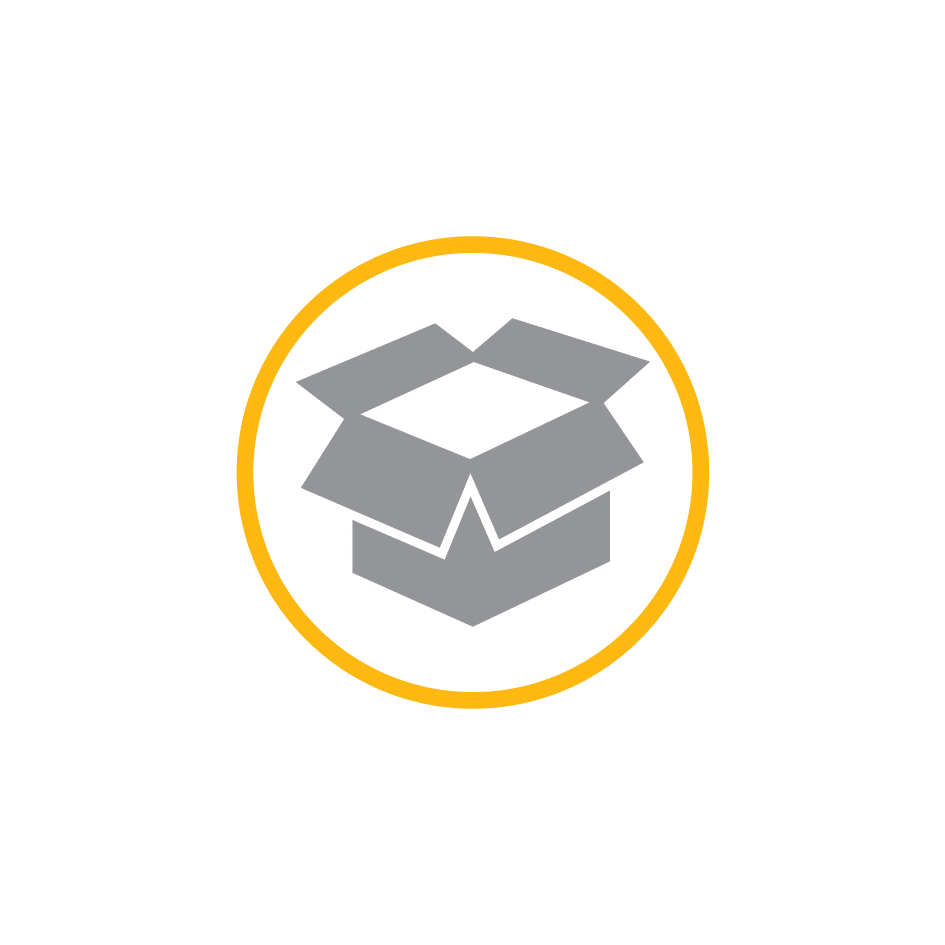
Filling and Packaging
- Definition of requirements according to GMP and EU standards
- Room layout
- Equipment selection
- Line automation including equipment integration
Equipment
- Pharmaceutical: Volumetric or gravimetric filling, dosing pumps, aseptic environment and equipment, RABS and isolators, bag and jar fillers, blister packs, cream and ointment pots and tubes, pick and place system, serialization, vision system
- Food and Beverage: Bottling lines, package thermoforming, filling lines for liquids, pastes, and divided solids, vertical in-line bagging, vacuum sealing, inspection system
- Packaging: Rotative or linear labellers, encoders, and printers (laser, UV, ink jet, etc.), safety seal applicators, buffer systems, cartoners, case erectors, flow wrapping, shrink film, palletizers, inspection systems
Optimization
- SCADA systems and line control, historization of critical parameters
- Equipment performance analysis and debottlenecking
- Compatibility review of equipment and packaging components
- Lean Six Sigma review of packaging operations
- Performance loss analysis and process start-up
- FMEA Analysis
- Optimization of overall equipment efficiency (OEE)

Clean Rooms
- Prefabricated walls, ceilings, floors, and doors
- Recessed accessories: windows, electrical outlets, indicators, lightning, etc.
- Integration of process, utilities and HVAC diffusers and return grilles
- Personnel and material air locks
- Laboratory and air lock furniture
- Sealing, cleaning, and decontamination
- Environmental monitoring
Architecture
- Laporte subcontracts all architectural work to a local and qualified architectural firm, ideally one that is familiar with the existing client installations
- Laporte’s engineers prepare the layout(s) of the production, electrical, mechanical, warehouse, and IT rooms

HVAC
- HVAC systems, dust collection, exhaust fans
- Hot water and plant steam heating
- Chillers, cooling towers
- Energy recovery
- BMS specification, integration
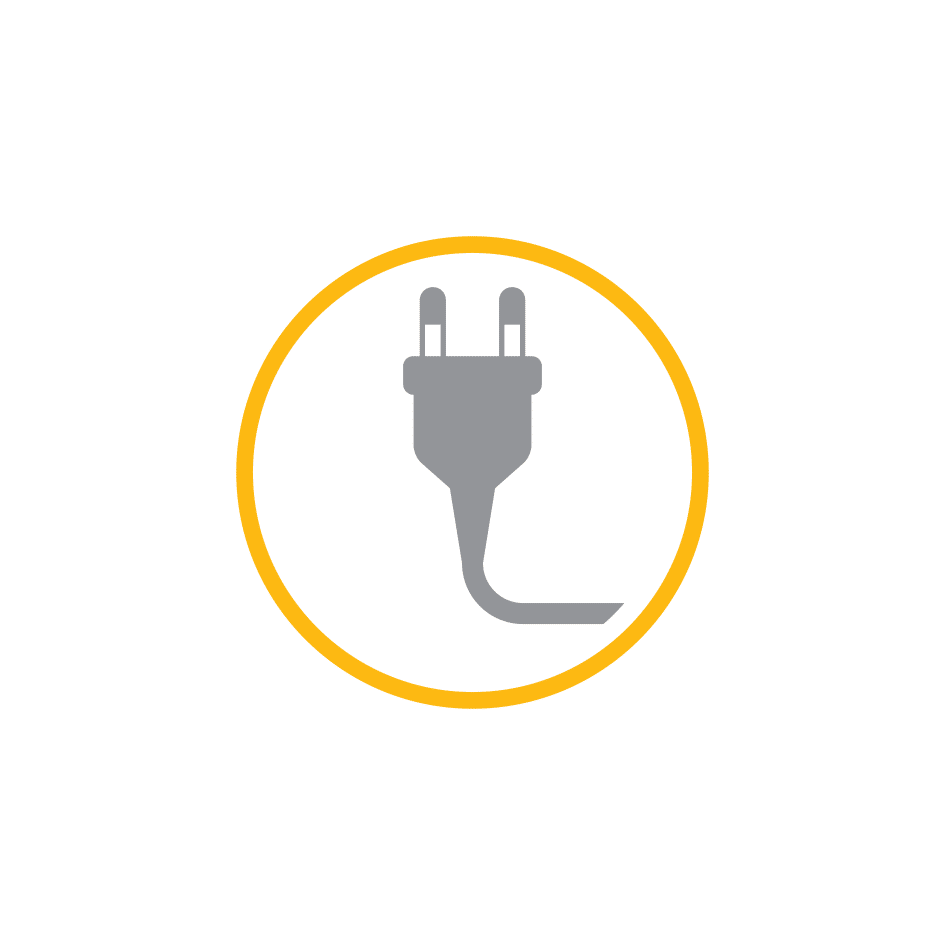
Electrical
- Design of electrical service entrance and low and medium voltage distribution (underground and above ground)
- High and low resistance grounding distribution systems
- Grounding grid design
- Uninterruptible power supply (UPS) and emergency power supply systems (generator)
- Building electricity (distribution, lighting, lighting control system, specialized equipment power supply)
- Fire alarm system design
- Access control systems, security alarm systems, video surveillance systems design
- Motor control center design
- Specialized studies:
- Classification of hazardous location for electrical installations (gases and dust)
- Protection coordination study
- Harmonics study and mitigation
- Arc flash study

Utilities
- Clean gases, clean compressed air, steam, water for injection, and instrument air
- Plumbing and piping
- Sanitary, storm and process drainage
- Effluent treatment and neutralisation
- Fire protection

Industrial Refrigeration
- Design of industrial refrigeration and heat pump systems
- Ammonia refrigeration systems
- Direct expansion and recirculated CO2 refrigeration systems
- Low GWP synthetic refrigeration system conversions and design
- High temperature ammonia heat pumps
- Custom chillers
- Product freezing and chilling
- Design of commercial refrigeration systems
- Walk-in coolers and freezers
- Precision temperature chambers
- Environmental chambers
- Reports, audits, and support
- Energy audit and reporting
- Energy management planning
- Feasibility studies and system capacity assessments
- Start-up support
- Troubleshooting
- Ammonia and refrigerant safety
- Process Safety Management (PSM)
- Regulatory and code compliance support
- Risk assessment and HAZOPs
- Mechanical integrity audits
- Standard Operating Procedures development
- Dispersion analysis
- Incident Investigation and Root Cause Analysis
- Markets
- Food processing
- Cold storage
- Breweries, wineries and dairy processing facilities
- Chemical processing
- Pharmaceutical storage and processing
- Mission critical applications
- Ice rinks and recreational facilities
Civil and Structural Engineering
- Laporte subcontracts civil and structural engineering to a local qualified engineering firm, ideally one that is familiar with the existing client installations
- Bioindustrial projects executed by IPSB (a Laporte subsidiary) are an exception, and they are handled in house

Health and Safety
Machine Safety:
- Risk analysis (CSA Z432 and ISO 13849)
- Electrical and automation safety circuit design
- Equipment upgrades and improvements
- Safety Instrumented System (SIS)
- Guarding and equipment protection
- Equipment conformity assessment
Process Safety:
- Risk analysis (HAZOP, FMEA, DHA)
- Flammable and combustible liquid and dust explosion analysis
- Electrical classification for explosive dust and vapour environments (NFPA 497, 499)
- Design of explosion prevention systems (NFPA 67, 68, 69)
Plant Health and Safety:
- Workplace safety and prevention program development
- Arc flash studies (CSA Z462)
- Electrical safety (NFPA 70E)
- Lockout/tagout procedures
- Emergency action plan
- Safety showers, liquid retention
- Loading and unloading hazardous liquids
- Workplace safety training
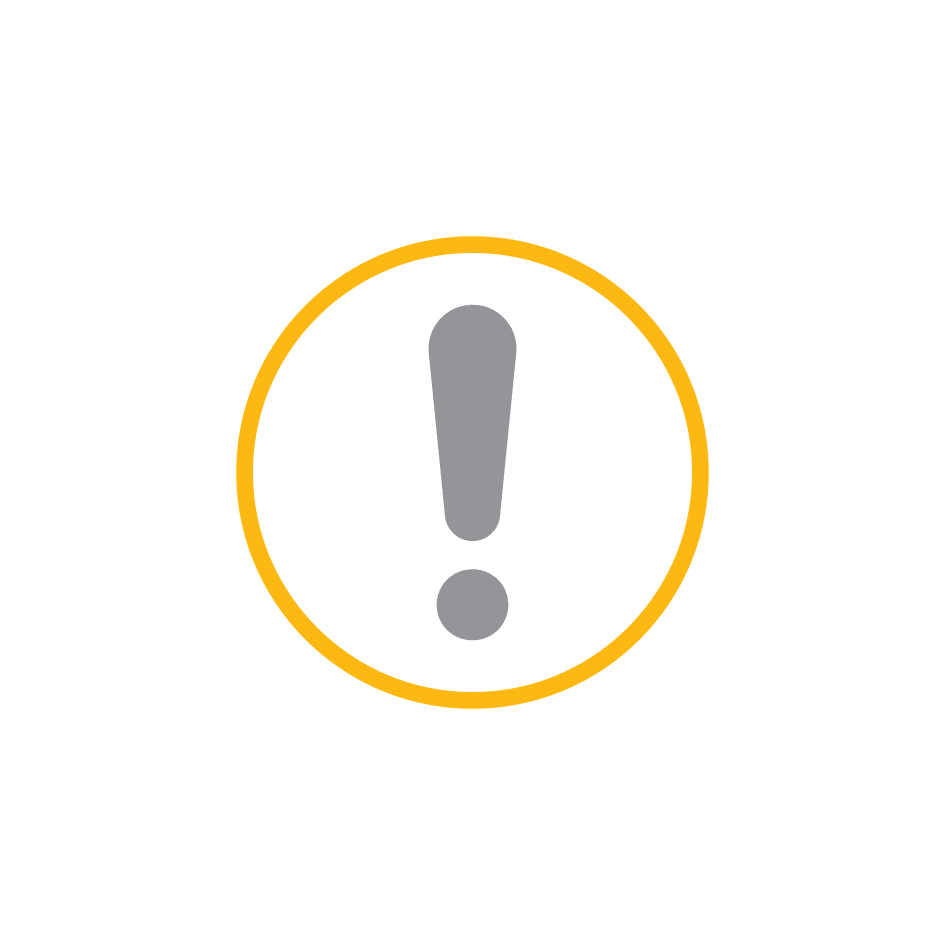
Industrial Risks
- Technical and regulatory expertise in European bioindustrial project risk analysis
- For more information, please visit https://ipsb.fr/en/. IPSB joined Laporte in 2019
- Regulatory positioning study and plant layout
- Building permits and operating licenses
- Regulatory compliance audits
- ATEX zoning recommendations
- Techno-economic studies of Best Available Techniques (BAT)
- Risk analysis
- Thermal, pressure, and toxic effect zone modelling
- Notification and site close-down procedures
- Demolition permits

Environment
- Carbon footprint
- Domestic water consumption measuring and monitoring
- Boiler room optimization
- Building upgrades and maintenance
- Ventilation and refrigeration diagnostics
- Building automation system (BAS) control improvement
- Environmental monitoring system (EMS) design, improvement
- Make-up air preheating
- Effluent energy recovery
- Electrical power factor and harmonic load calculations
- Process optimization and energy recovery
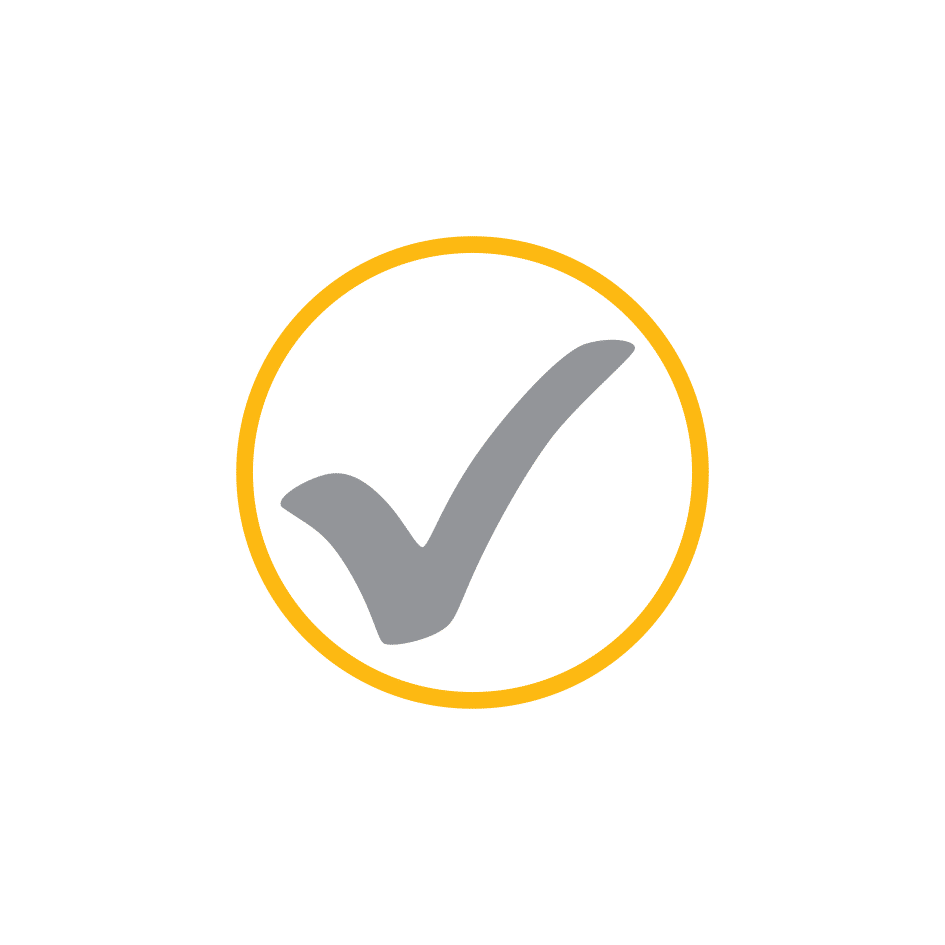
Validation and Regulatory Compliance
- Risk-Based Approach Validation Master Plan (VMP)
- Commissioning/Decommissioning and validation documents
- User Requirements Specifications, Functionality and Design Specifications; (URS, FS/DS)
- Installation, Operational and Performance Qualification protocols (IQ/OQ/PQ)
- Critical Utilities Validation, Manufacturing and Packaging Equipment Validation
- Process Validation and Cleaning Validation
- Computer System Validation, Data Integrity, and Track and Trace Validation (GAMP5)
- Conformity and GMP audits, GAP Assessments and Remediation Plans, Project Management, and Training
- Development of Quality Systems and Quality Manuals, implementation of Quality Programs and SOPs, Annual Product Reviews, and support for maintenance departments
- Expertise in regulations for Canada (Health Canada), the United States (FDA), the European Commission (Eudralex), and the International Organization for Standardization (ISO)

Food Safety
- Food safety control, zoning, and hygiene
- Assessment and remediation MAPAQ, HACCP, RSAC, GFSI, SQF, ACIA, FDA
- Inspection systems: vision, bar code reader, checkweigher, x-ray, and metal detector
- Food traceability
- Cold chain control and monitoring